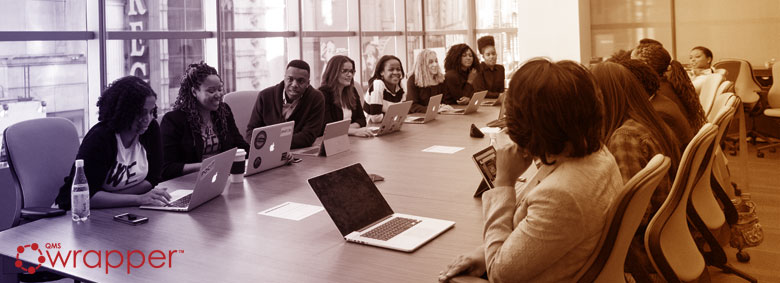
How to do an Offsite Audits
An offsite audit is the same as an on-site QMS audit, but the auditor engages with you via technology.
The Initial Preparation
Prior to starting the offsite audit, most likely you, a medical device company, would need to provide copies of your quality manual, procedures, complaints, nonconformance, corrective and preventive action logs, etc.
Also, you will have to include a facility map of your MedDev Company. It should involve the buildings and grounds, infrastructure and equipment layout, storage, maintenance, receiving, shipping, and other areas as appropriate. The map can help plan the route for the virtual facility tour.
A Necessary Element of The Audit
When it comes to the audit, you will need one of the online platforms with screen sharing that you can use for the meeting.
Once the opening meeting is completed, it is time for the virtual tour of the facility to use the preplanned route based on the map is provided. There a lot of platforms helping with this.
The auditors will probably take into account detours due to maintenance and other unforeseen activities.
From A Virtual Tour Back to Paperwork
Once the virtual tour is complete, the next is to review the complaint, nonconformance, corrective, and preventive action logs. This will determine what processes and production records will be reviewed during the audit.
At this point, the medical device company is processing the records request. Using eQMS and screen sharing can be very easy. The auditor can check the document immediately.
Examples of A Possible Scenario
Let’s imagine the situation the auditor is asking to preview the last management review meeting details. Having the process based eQMS, the company will be able to filter complete work per process (selecting the asked) and to show all details through the entire workflow with the actual output – documented record about the management review meeting.
Let’s imagine a bit more complex situation when a member of the design and development team will be audited. The auditor may ask about complete device design and development life-cycle. Having the tool in eQMS for organizing this stage will make the audit easier.
It is usually handled through traceability matrix features. All the documentation is sorted out and managed from one place. It’s easy to provide the required record on auditor demand immediately, in front of his eyes.
When it comes to manufacturing processes, the offsite audit can be a bit demanding.
A virtual tour of the process may be conducted, preferably for the part produced in the batch record. This would be a time to conduct a virtual interview of the process operator and quality inspector to verify what has observed in the records and that the work instructions reflect the actual work practices.
Offsite audits, which leverage technology such as video conferencing and screen sharing to conduct interviews and share documents and records, are a practical alternative to ensure continued compliance with GMP requirements in extraordinary situations.
Juliette B.
|
Juliette B.
|
Juliette B.
|
John Broomfield
|
So, instead of interacting with job floor workers as they do their work they have to step away to a quieter room for the interview.
This becomes stilted conversion for both the auditee and the auditor who will want to ask "please show me".
This is a problem yet to be solved.