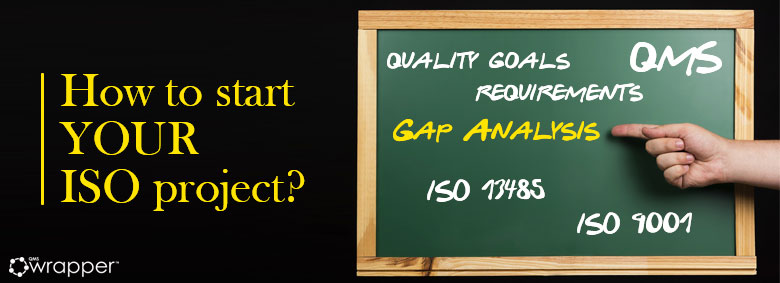
Gap analysis in QMS
Perfect, now when you have learned about the ISO 13485 standard with the help of 20 lessons explained on this website, now you are ready to implement it. The first step is to perform a GAP analysis. We won't leave you hanging at this part now, so we explained it to you as well.
You might wonder how can serve you a Gap analysis?
Gap analysis for the Quality Management System sort of works like a map. The map that provides not only a starting point but a direction, significant relation along the way, and final location.
In translation, it’s a practice that serves as a comparison of actual performance or results with what was expected in your company.
By applying Gap analysis, you will have to identify incomplete or missing strategies, processes, structures, capabilities, practices, and then recommend steps that will help your company to meet goals. Also, it can be used to enhance individual or team performance, and look at characteristics such as task competency, performance level, and productivity.
For example, you want to identify what do you need to do to meet the requirements of the ISO 9001 or ISO 13485. In that case, the best practice is to do a Gap analysis. You can find certain Gap report tools to help you reveal any “holes” between “what you currently do” and “what the compliance standards are expecting”, to help you identify missing or incomplete processes.
If it's done well, it will significantly save you time, money, and resources.
How to
When you want to perform a gap analysis, you can give that responsibility to some of your employee that has some more quality management experience, or another way is to hire a consultant or use a tool for it.
The Gap analysis as a strategic management tool
Certain activities must be carried out to perform a gap analysis.
- Setting quality goals
- Assessing current quality levels
- Calculating the gaps between the current level and goals
- Planning to overcome the gaps
The Gap analysis as a checklist
You can create one yourself or purchase it online. It's crucial to layout the certain ISO requirements into a series of steps. Having a checklist will help you stay on task and focus on the elements required for ISO certification.
Note: By purchasing a checklist, you will save time because they are already carefully prepared; they are written by ISO experts that ensure you that nothing has been left out.
Process of a Gap analysis
If you hire a consultant, he/she will be asking your employees about QMS in your company, so you need to make sure they are prepared to respond adequately.
If you doing it by yourself, inform your employees in advance when you plan on conducting it, so they will get themselves ready. Split your business into sections to be analyzed. Take your checklist and you are ready for actual gap analysis.
Keep in mind, while analyzing keep your focus on the present, therefore pay attention to processes you have in place currently, and not the ones you plan to add in the future. With pen and paper in hand, while going through company sections, take notes on your findings as you go through the analysis.
Don’t get confused while conducting the gap analysis, it has to show whether your current QMS meets certain ISO standards, not whether or ready for certification.
Quick overview:
When you will carry out a gap analysis, you will generally:
- Compare the requirements of ISO 13485 to your current QMS
- Document how your current system complies and does not comply with ISO 13485 requirements
- Based on the results of your gap analysis, determine what to include in your implementation plan
Once you complete a gap analysis, you will generate a report that involves:
- The areas in which your company meets the standard's requirements
- The areas in which your company is not complying with the standard's requirements
- Recommendations of what to include in your implementation plan
QMS Tags
Upgraded Dashboard and QMS Control
ISO 9001 implementation: Mandatory documents and records