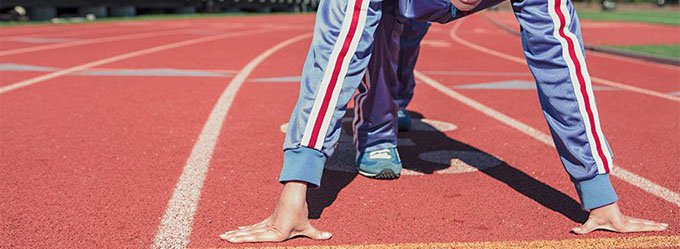
QMS for Beginners – A quick guide on where to Start ! …Part 1
Whether you are freshly minted into the QMS position or you are a founder of a Startup or a product manager with a new project, you’re reading this because your strategy requires QMS oversight and your first question is likely "Where to Start” and “What to Do”
We could squeeze in 5 main points the initial mindset that will help you bootstrap your QMS efforts:
- There is a lot of information on the Web, but it is not all very helpful. The danger resides in fluff internet info pieces, written for promotional purposes. Look for the conscientious experts, the topic has been discussed in the article Expert vs Expert.
You are not alone and you are not the first. So, start with the mindset that you will make mistakes – but they can be fixed. The important thing is to learn and keep moving the team forward.
- The company’s priority is sales, not QMS. So, live with it! Companies have products that need to be sold and that’s the #1 priority. The role of QMS is to ensure that those products are produced -- with quality, AND SOLD TO CUSTOMERS.
- QMS is about the customer, not QMS. If you do it right, it's not a burden. QMS done right is not an added layer of management that gets in the way. QMS is about responding to customers, to problems and making it right! Your motto is “Get it right the first time”.
- For QMS to succeed, the founder/president/CEO/CTO/CFO, the top leader, top dog should be involved and bless this initiative and get quality reports.
Where to Start and what to do when you need to implement a QMS?
The following 13 items will guide you:
1. Figure out what QMS you need
What is it you need? FDA QSR, ISO 13485: 2003, ISO 13485: 2016, or ISO 9001: 2015.
Secure a copy of whatever Standard you intend to be compliant with, and get at least a bit familiar with it… you need a general idea of what is expected, why and very importantly get a feel for the technical language they use. If you are a real keener you can learn all the details. Otherwise, read on… there are easier ways.
Care should be taken as more than one ISO can apply or be connected. For example; if you are following FDA QSR or ISO 13485: 2016, they are based on principals of Risk Management, so you also need to secure a copy of ISO 14971 Risk Management.
2. Designate a QMS Manager (unless that’s you)
Designate someone as the QMS Manager. Likely you are a founder and you don’t want to do it yourself – really, you do have higher priorities. Find someone who enjoys administration and documentation -- yes, they do exist! They can then start to make your QMS a reality. But don’t think you can escape this, no! no! no! You’re going to have to stay involved, especially in the initial phases to ensure QMS is “seen” as a priority, and you need to keep it front and center -- everyone else will want to lock the QMS Manager in the closet… because QMS is not their priority, Sales are. But compliance and either your 510(k) or ISO certification depends on it…
So, plan ahead now, when it's easy, not later, when it’s much harder.
3. You will need a QMS manual
Various ISO standards and FDA QSR’s require that you have a QMS manual. In the QMS manual, you will outline the various policies and procedures that your company and teams will follow to produce quality outcomes. This will include how you will measure quality, Define Risk, make and define how to correct mistakes and prevent them from what actions (CAPA or Corrective Actions, Preventative Actions), etc...
The QMS manual will also define the various roles that are needed within the company such as who will do what, and how. For example, QMS Manager, but also what role unit managers will play.
The QMS manual then becomes your “go-to” book on what to do. You’ll also need to keep it up to date. Not an easy task.
The GAP Analysis
Here’s the critical element. You should also realize that the QMS Manual drives the GAP Analysis. It will point out the differences between what you said you would do to ensure Quality outcomes and the processes that you execute on and what you have done to ensure Quality outcomes. The GAP is what you are missing!
qmsWrapper GAP Analysis has 2 advantages:
When you subscribe for a 12-month subscription of qmsWrapper, the QMS Manual and the GAP Analysis Module (checklist) is included. Not only does this represent a huge saving in costs, but they can also be very pricy to buy directly, the real cost, however, is in time – yours and your teams.
The second big benefit of using the QMS Manual from qmsWrapper is that it is integrated into and throughout the qmsWrapper software. What you document in the QMS Manual is reflected in the qmsWrapper application, in particular through the QMS Workflow processes. So, what’s in the manual is executed in the Workflow processes.
But wait, there’s more. Both the Manual and QMS Workflow processes are integrated into the GAP analysis Module (coming soon).
If you want to know how significant this issue is, read any blog on Gap analysis. But bring a heater, you’ll go cold in fright.
For a full understanding of the benefits, read on.
To be continued …
QMS for Beginners – A quick guide on where to Start ! …Part 2
QMS for Beginners – A quick guide on where to Start ! …Part 3
QMS for Beginners – A quick guide on where to Start ! …Part 4
A New Vision for Risk-Driven QMS with qmsWrapper
qmsWrapper Recognized as a Rising Star in the Spring 2025 Quality Management Software Customer Success Report
Enhancing Visibility and Accountability in QMS with qmsWrapper’s New Log Functionality