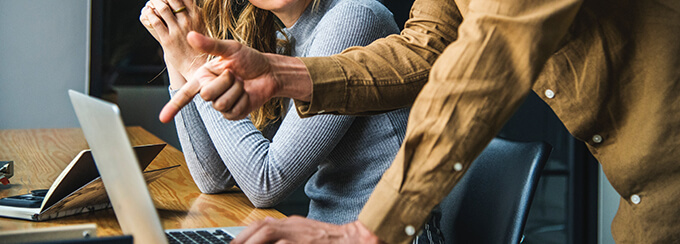
Choosing a QMS system? Why you should seriously look at the new qmsWrapper!
The new version of qmsWrapper is updated in December 2019.
We were still shaking from a disastrous ISO audit. Joe, the perennial QMS manager from Jurassic times, just have been fired. Even though he liked pushing the paper-based system, a medical device company has too many regulatory pitfalls to trip you up. Brilliant engineers and developers just didn’t understand.
The next in line, I was now the new “freshly minted” QMS manager. I love my job. I didn’t want to lose it! So how to avoid a similar Jurassic outcome? How to avoid future disasters? As I looked across the boardroom, you could feel the disappointment. Delay is not the friend of a startup and attracting funding.
The big cheeses were all there, their dreams of an early CE mark had crashed and burned in a flaming inferno, and now the 510(k) seemed like a rudderless boat in a storm. There didn’t seem to be any way to ride the waves. Although a bright sunny day, no amount of light could penetrate the gloom in that room.
Our company designs and develops medical technology for the early detection of heart disease at the clinical level. An approved device was essential to the survival of the company. The genius engineers had one big set of obstacles, regulatory compliance, and standards. I was given carte-blanche. We don’t care how you do it, just get it done!
THE CHALLENGE – Lack of experience, teams in multiple locations, and no automated QMS system.
Don’t panic!
Good advice, but easier said than done as I had two huge concerns.
First, how to harmonize our company’s product needs with the quality standards without any real-life examples and without any previous experience. My greatest fear, the blind would be leading the blind.
Second, we had one team in North America with the second team of engineers and medical experts in Europe. I cannot always communicate with them face to face and I was worried that managing QMS for two separate teams, in two different time zones – the documentation alone would be a nightmare. Try to imagine five managers, located on two continents, having to approve one document - Email, print, scan, sign, circulate, repeat, repeat, repeat, repeat! Oh, the joy!
There had to be a better way?
I knew that it would be extremely stressful and time-wasting staying paper-based. Sure, for a two-person company, it might be possible, (well, still not the best) but for us, this was not a realistic option - we needed an electronic QMS that would fit our needs, that would fit our culture, that could unite us, not divide us.
THE OPTIMAL SOLUTION – Cloud-based, integrated QMS solutions specific for medical device companies
So the search for the optimal and best eQMS software began.
Our starting point was that any solution we chose had to be validated for use. It’s a fundamental issue for both the FDA and ISO standards. So, that was the start point.
Next, the requirements were broken down into three categories of functionality;
1) Must have; required for regulatory compliance
2) should have; stuff that would make it work reasonably well.
3) nice to have; things we could do without but if available we would add
There were 9 “Must-Have” functions:
- Controlling Documents, with versioning, history, active status and approved status and a document vault.
- Need to support Workflows, Procedures, SOPs, and Processes. Must have the ability to create new ones and edit existing. Existing processes should include all already proven and approved processes for ISO certification, so we don’t have to reinvent them.
- Approvals system with electronic signatures, showing who approved what, when with proof of a unique ID. Approvals should be for documents, reports, processes and any forms we use.
- QMS progress overview of the various stages and steps in QMS workflow processes.
- Exporting to Excel for all manner of reporting.
- CAPA tracking system, showing what needed to be fixed, who was assigned to fix it, and what was fixed.
- Support for Risk assessments conformant with ISO 14971
- Has to support both FDA CFR’s and ISO 13485 compliance.
- It has to be affordable. Likely, the most difficult of all. We were a startup, not a corporate conglomerate.
There were 7 “Should-have” Functions.
- Electronic Signatures, would make it easier but we could always do real signatures in a pinch, they had to meet FDA CFR part 11
- Document vault, for regulatory approved documents that cannot be erased or modified.
- Electronic forms, saved to a database so information is not lost in documents but is searchable in a database.
- The search tool, to find any document, form, task, process and exportable to a spreadsheet (preferably Excel). We want to create our own print reports through excel not be limited by pre-existing report formats.
- All the forms required for ISO 13485 compliance should be included and easy to adapt and customize to our needs. As we were in-between the old 13485:2003 and the new 2016 version, the forms for both standards should be included. We wanted to be certified for both ISO 13485 standards and in full compliance with FDA CFRs.
- Controlled access to various parts of the system based on roles and permissions.
- Ability to capture into user communications as proof of completion for any QMS related issue
There were at least 6, “Nice-to-have” functions: (this list was cut short, we could only dream).
- Integration into a project management system.
- Integration into a Workgroup communications (chat) app.
- Dashboard, showing all active tasks that need to be done and the status of review items.
- Tasks lists, also ToDo lists.
- QMS manual.
- Traceability Matrix
With our shopping list complete, we started our investigation. We reviewed and tested many possible solutions.
Some were pure documentation based – a zip containing all manner of forms that was provided and you used them as required. The issue was that nobody understood what form to use when. This approach was rejected wholesale as unworkable and disaster in the making. There would be no manual system.
New requirement. Processes should drive the workflow so users don’t have to, and users cannot ignore it.
We continued.
Now the problem was that many systems were huge, targeting large and medium-sized companies, in particular, pharma. Not only would it take months and months to implement, but the task of training people itself would be difficult. They were also very expensive. Forget using it! We had a budget, not a gold mine. They really were not for us, we’re a medical device company. Not going to happen! Rejected!
Some of them were obviously ancient systems built over DOS (remember that) over many, many years. Very complete, just not very useful or user-friendly. I never really knew what MS-DOS was until then. There was also the version that had some windows UI slapped onto a DOS system. Lipstick on a pig. Cute. Retro rejected!
Then we started getting into the more recent systems. Some included a risk module, some not. Some had QMS management, but not integrated into project management. So, all QMS activities had to be re-entered manually. These were the specialist tools, good at 1 or 2 things but that was all. The reality was that there was always some essential functionality that was missing. It was beginning to look like we would need to use several separate tools to get our essential must-have functionalities. Divide and conquer looked more and more like a support nightmare.
Surprisingly, the most difficult items on our shopping list were the “nice-to-have” items. None had a QMS manual. None integrated into a project management application. In some, Workgroup communications existed, but you had to buy separate licenses for each user. You could expect to create a file and keep it in QMS but not integrate it into the QMS. The connections were missing. The integration would be difficult.
The hardest functionality to find was the Traceability Matrix. It was becoming clear we were looking at going back to Excel as our primary matrix app. There were 1 or 2 other apps out there, but they are no better than a basic excel table. To get our TM, we would have had to enter all the inputs manually, and the result would look like a TM, not work like one. Not very beneficial for the long term. So, it looked like Excel it would be, at least we knew how to use.
Lastly, back to a core issue, the cost. They were all very costly. The keyword is QMS, and the price shoots way up. Buy one module, ok, buy more, NOT cheap! We thought we’d have to sacrifice functionality for affordability. For a start-up, that is not a good option.
Fortunately, after this insane and intense search, we found a solution that actually met most of the functionality on our shopping list. From must-have to nice-to-have, and it was really affordable. So affordable, that at first, we were highly suspicious of it. Was it too good to be true? To our great surprise, it turned out to be the real deal.
But it was from a new guy! Oh-oh! We had to be convinced they were in for the long term. (that was over a year ago they are still going strong).
Our best QMS choice, by far, at this point was qmsWrapper™.
A little history on these guys. The qmsWrapper was created by a medical device company for themselves because they could not find suitable software that combined project management and Quality Management, specifically for regulatory compliance. The name Wrapper comes from the fact that they tried to “wrap” a QMS around project management software. The idea was that they didn’t have a large admin team to do all the compliance required stuff; they were software and hardware engineers and doctors, not paper pushers. So they designed and built the first version of the software to combine development and compliance – they invented it!
Then when others started asking to buy the software they spun it out into a separate company and so qmsWrapper was born. Because the understood the startup's pain of bootstrap financing, they made it very affordable. They too were a start-up and understood the start-up's pain.
qmsWrapper the software is now in version 6.0 It is no longer the simple software of two years ago or even last year. They’ve made huge improvements, but still, there was this nagging feeling that it might be too cheap. Was it cheap? Or affordable amazing cheap? Was it too good to be true?
Officially, it’s a cloud-based development and compliance management software, in layman’s terms, a QMS and Project management system specifically designed for medical device companies, including start-ups.
So, we took the plunge and did the 21-day trial. It was a disaster! But, knowing there was nothing similar out there, we arranged for a live demo. They sorted their demo trial out and amazing things started to happen.
What initially surprised us, was that it only took a few days to implement and train our people on how to use it. Then we started to appreciate the benefits of a fully integrated system. You’re not running different applications – engineering is connected to compliance – WOW! What a mindset change that was.
Back to our essential functionality shopping list. Tick, tick, tick… The must-haves, should-haves and even the nice-to-haves all seemed to be there, and much, much more.
Over the last year, to our great joy, they continuously improved the app, adding eForms, an electronic vault, and eSignatures. They also improved the “approvals” system, even adding approvals for both processes and forms. This was really starting to smell of compliance.
Next, they released a QMS Manual and GAP report tool. This allowed us to create our own QMS Manual, fully integrated into all the modules, including the QMS modules and the processes. The process included in a project will automatically be included in the quality manual. We never had to worry about our quality manual is out of date again, and with our audit pending, we knew we had it covered. With the qmsGap report tool, you can see exactly where you need to focus – before the audit!
Recently, we received the beta of the Traceability Matrix. This thing rocks. The project manager for the hardware device is already using it, and she says it cut her workload by half, but also her long-term workload for ongoing development and lifecycle management also by half. Her amazement is that she can control her project through the TM. She’s already done a few dry runs for her FDA 510(k) submission and she is amazed that she can export it out to Excel and print it all out! (and create the eCopy for FDA). She said, compared to using Excel to create her TM as in the past, this TM is alive! And for my Christmas present, it’s fully integrated into both the QMS and into the project management module so when you update a task in the either the QMS or the project, it gets updated in the TM. How cool is that!
The flexibility and utility of qmsWrapper are truly amazing. In our current clinical study, we even used the processes and the eForms to create medical processes for the doctors and nurses to follow. They found it very easy to use and understand. We were able to collect our medical test data flawlessly, and to avoid the dreaded “missing data curse”. Imagine a clinical study with little or no missing data. Awesome! For a startup like us, being able to use the processes like that, really made it easy for us, it almost felt like we were cheating!
State of affairs so far: we have one 510(k) approved (Cleared), five FDA Q-subs, one FDA DeNovo in progress, another 510(k) in progress, with two CE applications in final stages. One consensus study, one clinical investigation starting September 1st. and ISO 13485:2003, ISO 13485:2016, and we figure we’re fully FDA CFR 820 compliant.
How can we handle all of this? qmsWrapper!
We can handle this monster workload because development and compliance are supported and facilitated by the QMS system, not hindered by it.
qmsWrapper is like a level of QMS management, meaning you don’t have to add a lot of staff to do your compliance work because it's already integrated into the project management. I could go on for some time.
qmsWrapper is cloud-based which was another benefit we had not expected because we don’t need our own hardware infrastructure to support it. So much easier!
It’s hard to fully appreciate all that qmsWrapper has to offer because it is so very complete.
The proof of its benefits was how we handled the fear of an ISO 13485 certification audit. That is the proof of the pudding as they say. But that is another story.
Having looked at the apps out there and now having successfully experienced an ISO audit with it, you should really take a look at qmsWrapper. We looked everywhere and found nothing better, even when compared to bigger and more established, and more expensive systems.
qmsWrapper is a lot of value, so you might have to give it an honest try to fully appreciate all it has to offer.
Drazenka N…
QMS Manager
A New Vision for Risk-Driven QMS with qmsWrapper
qmsWrapper Recognized as a Rising Star in the Spring 2025 Quality Management Software Customer Success Report
Enhancing Visibility and Accountability in QMS with qmsWrapper’s New Log Functionality