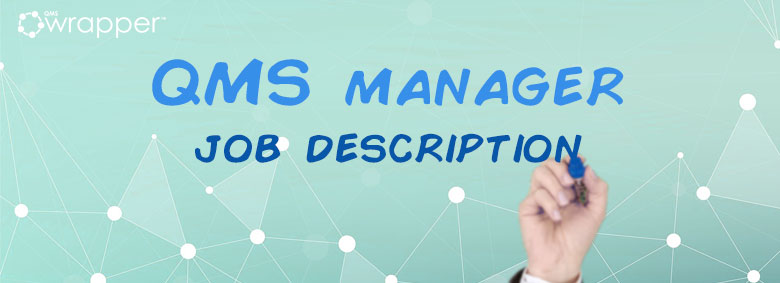
QMS Manager role in MedDev industry
ISO 9001 sets out the criteria for a quality management system.
Quality Management System (QMS) ensures that an organization, product or service is consistent. It is a collection of business processes focused on consistently meeting customer requirements and enhancing their satisfaction. It is aligned with an organization's purpose and strategic direction.
It is expressed as the organizational goals, policies, processes, documented information and resources needed to implement and maintain it. It has four main components: quality planning, quality assurance, quality control, and quality improvement.
ISO 9001 specifies responsibilities for management in the quality management system, and it’s adapted to specific sectors and industries. It includes also ISO 13485.
ISO 13485:2016 specifies requirements for a quality management system where an organization needs to demonstrate its ability to provide medical devices and related services that consistently meet customer and applicable regulatory requirements.
Related to this: ISO 14971:2007 specifies a process for a manufacturer to identify the hazards associated with medical devices, including in vitro diagnostic (IVD) medical devices, to estimate and evaluate the associated risks, to control these risks, and to monitor the effectiveness of the controls.
The first pulls the second.
QMS focus
Quality management is focused not only on product and service quality but also on the means to achieve it. Therefore, it uses quality assurance and control of processes as well as products to achieve more consistent quality.
It sounds like a tough and extensive job… No wonder it requires at least one person to deal with it!
What does a QMS manager do?
A QMS manager safeguards that standards are met throughout all processes of the company, from customer relations to manufacturing processes and all in between.
A QMS manager is expected to provide instruction regarding company policies, standards, processes and practices and to ensure all employees follow company procedures in accordance with their role.
When it comes to the Medical Device Industry, the responsibility of top management is to ensure a QMS that is built in accordance with the structural requirements set forth in 13485:2016.
The responsibilities may include the following:
- Develop quality control processes
- Create and sustain the up-to-date product or process specifications
- Understand standards applicable to the business and ensure that they are met
- Train employees on quality assurance standards and processes
- Supervise the work of managers over various sectors
- Give instruction when standards are not met
- Check product development and manufacturing processes to ensure quality standards are met
- Identify quality improvement opportunities
- Provide quality reports
- Perform internal audits over the company’s quality systems
QMS manager requirements
To be qualified for a QMS manager position, it’s desirable to have a bachelor’s degree in a field related to quality control such as business administration or quality control management. Strong analytical skills to filter key points from complex details and develop plans accordingly and problem-solving skills are a must. They should be familiar with the methodologies, tools, and concepts of quality management. Also, they should have the ability to communicate the knowledge of industry standards to others. QMS managers should be able to interpret statistical data.
QMS managers need to have the following skills too:
- Effective communicators and excellent motivators
- Negotiating skills
- Report writing skills
- Excellent planning skills
Certain companies expect their QMS managers to have a thorough knowledge of the specifications that relate to their specific business. For such cases, they're a lot of ISO training available. Even online…
QMS managers integrate their knowledge and expertise in order to accomplish set goals and always begin by first understanding and establishing their role and relationship with line staff. They play a crucial role in business by ensuring that products meet certain thresholds of acceptability. They work to improve an organization's efficiency and profitability.
Kelly R.
|
Carole Smith-Pitt
|
Thomas
|