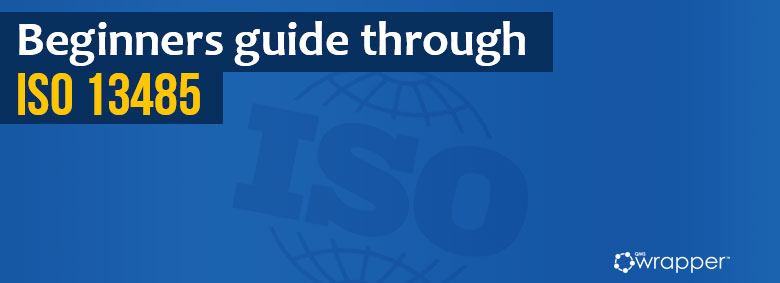
5 FAQs about ISO 13485
1. What is an ISO 13485?
ISO 13485 is an international standard for establishing quality management in the medical device industry. It is an effective explanation to meet the comprehensive requirements for a QMS in the medical device industry.
The other well-known QMS requirements to follow come from the US, as the FDA requires that the medical device company complies with 21 CFR part 820.
2. What is the current version of ISO 13485?
The latest revision of ISO 13485 for QMS in medical device companies is from March 2016.
3. Does ISO 13485:2016 only apply to medical devices?
ISO 13485 was specifically created for companies working on the medical device field. It can be applied to organizations involved in one or more stages of the life-cycle, including design and development, production, storage and distribution, installation, servicing or final decommissioning of a medical device, disposal of medical devices, and design and development or provision of associated activities (e.g. technical support).
The Standard can also be used by suppliers or external parties that provide products, including QMS-related services to such organizations. The supplier or external party can voluntarily choose to conform to the requirements of the Standard or can be required by contract to conform.
4. The company received ISO 13485 certification; does it mean it can place the medical device at the market?
No. ISO certification doesn’t mean automatic regulatory clearance for the product, it simply means you have a compliant QMS, which is the first step in getting regulatory clearance for the device. Various jurisdictions have different processes for regulatory clearance for medical devices.
5. Why should medical device companies have a QMS?
The practice of implementing a QMS is a long-term tactical decision that, once in place, works to guide the company to constantly meet standards, improve general performance, and to provide a basis for maintainable development initiatives. A QMS also gives assurance to customers that the requirements for quality have been met.
ISO 13485 implementation: Mandatory documents and records
Validation efforts
Gap analysis in QMS