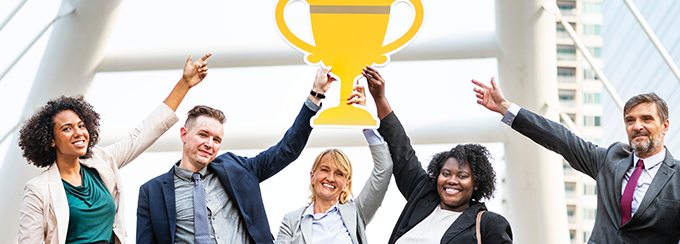
Audit Day Fears are Gone! How Cardio-Phoenix carried out of an ISO Audit With Help from qmsWrapper
Audit – a word that inspires anxiety. Even when everything is well planned, and you think you are prepared, anticipation turns to anxiety, anxiety to fear, and fear to panic. There is no hiding anything in a remote closet or under the carpet.
“Wherever you've hidden it, we'll find it.”
Audit Senior
It's an audit day!
In the beginning, there was fear.
The story starts with a medical device startup, who designs and develops a medical device for the early detection of heart disease at the clinical level.
Drazenka N. the Quality Manager and her team awaited the scheduled ISO 13485 audit. The past audit still hunts them. It was horrible and they can still taste the bitterness of that day.
One big change was made, they deployed a new QMS system, qmsWrapper™.
Going into this audit somehow seems different. The printer is cool. There is no last-minute rush around for signatures. Paper is stacked in ample supply, waiting. And wait it will, for it will not be involved in this audit.
This is their story …
Now with confidence.
The auditors are having breakfast at the hotel. We waited, anxiously. Last year was a disaster, and the QMS manager got fired. Now, they were coming again.
But something was different this time. The team seemed less nervous. There was some dust of fear but nothing like last year! Were they prepared and ready to go? Last year’s auditors saw the conference room turned into mountains of paper, neatly stacked, ceiling-high, or so it seemed. But the feeling that this year was different could be seen now. At the conference room table was just a laptop with an extended monitor. The boxes of files and mounds of papers were missing.
They arrive, shaking hands, greetings, recognition, coffees all around, nervous laughs… it’s about to get real.
Start-point, they ask to see the Quality Manual…
Click, click, click, and there it was on screen. The expected mounds of paper were replaced by an online version. It was perfectly organized according to the ISO 13485 standard - so neat and freshly updated.
We went through the entire Quality Manual simply clicking through it. Everything that they wanted to see, it's simply laid out on screen. “Are employees familiar with the procedures, are the standards followed, organizational chart, roles, and permission…. Approved processes, required by ISO 13485:2016 standard, all automatically updated by chapter number, mimicking the ISO 13485 quality standard.”
qmsWrapper as support of success.
They were stunned! Not only that everything was there, but it was all cross-referenced and updated right into the QMS software itself, and this cross-references into the various projects. QMS was not just a theory, it was there in the project files, connected.
Through qmsWrapper we were able to provide all the approved forms and processes that made ISO 13485:2016 possible, and smooth. We didn’t have to re-invent the wheel, just initiate and follow the processes and projects, and where was needed, just edit the existing ones or create some new ones. Managing the project was managing the quality. Every process is tracked, recorded, documented. everything has its own traceability.
Auditors wanted to know what processes were being used, and who initiated them and who approved them. We could easily demonstrate what processes had been initiated, when, what stage they were in, who initiated them and who approved them. Full version and approval control, with history.
With qmsWrapper it was easy to show them who is responsible, what is an obsolete document, and what do we do with them, which documents were approved, and which files in the vault for regulatory lock-down.
They wanted to know if we had done an internal audit and whether we had any proof for that? Did we have a follow-up meeting…, the answer, to the sound of a click, click, click… or yes, yes, and hell yes!
What the auditors wanted to know:
1. Who was responsible for documentation?
2. Who approved the documentation?
3. Was everybody familiar with the procedures?
4. Was everybody familiar with the quality manual (policies and objectives)?
5. What happens with obsolete documents, where do we store them?
6. What procedures (process or workflow) do we follow?
7. Who approves what processes?
8. Which version of the process do we use?
9. Why is something approved?
10. Where is the approved documentation stored?
11. Measurement and tracking
12. How any completed processes and who did what in them.
13. How many currently active processes do we have, and at what stage are they in?
14. What is traceable? Provable!
15. How do we manage our documentation in general?
Confidence restored. No fear now. Not only that we could show them the proof, but we showed them how it works right there on the spot.
Instead of 2 days, the audit started at 8 am, but by 11 am it was effectively over – you could see it in their eyes. 3 hours! Not bad!
They had gone through their entire list. Now, time for long, stress-free lunch, and by 2 pm they were well on their way home.
Stunned! Bedazzled! (it’s a really nice word for gapping mouth open in awe!). Not only them but us too.
During the certification audit, the Notified Body auditors, both with 20+ years in quality management and with 10+ and 6+ years as auditors, were tremendously impressed with how qmsWrapper helped us to integrate project management with quality management. They had never seen anything like it, not even in the big and super expensive systems.
Auditors were most impressed with the following
1. Processes and how everything can be tracked through processes, who does what, in what way, where documentation is stored, no skipped steps.
2. How easy it was to use, that everything was summarized and visible in one place which is a huge time saver.
3. CAPA’s. They expected issues with this part but were stunned with what followed, their trackability through completion. Because project management was combined with quality management. They literally took control of the mouse and clicked their way through the CAPA’s, showing each task and assignee proving that it was actually executed and properly completed or showing what stage of completion it was in! it was all trackable.
Everything was visible - trackable. Processes could be followed up to the person who completed the task. Approvals could be followed and tracked through each step. There was no form that could not be tracked to the source or initial task or requirement. Workflows were easy to follow and customize.
The road was clear for the submission of our CE mark application and our FDA 510(k). qmsWrapper, not only did ISO13485:2016, but helped us with FDA compliances as well.
We received both ISO 13485:2016 and 2003 certifications. The compliance was complete.
Sure, we have been prepared, but qmsWrapper was our secret ingredient that delivered our first Michelin star.
And No more will an ISO audit invoke fear!
FDA, bring them on! qmsWrapper has our back for this one too!
After the first disastrous audit, how did we end up with qmsWrapper? That is another story.
Adam Voltski
|
Jason M.
|