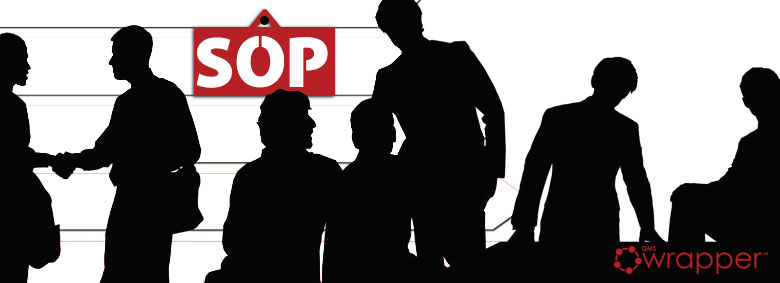
20 things you need to know about SOP for medical devices
So, you are a medical device creator and you reached to the point when you see that SOP (Standard Operating Procedure) is required by the FDA, ISO, and other regulatory bodies.
But what SOP actually means? By definition, it’s a document that describes the regularly recurring operations relevant to the quality of the investigation. The aim of the SOP is to carry out the operations correctly and always in the same manner. In essence, it should always be at hand in the workplace.
But in another word, we could put it this way. Standard Operating Procedures for medical devices are well-written instructions that specifically describe how each department should do a specific task.
Let’s skip to the main thing, and number up all the things you should keep in mind about your SOP:
- Try to be consistent with the format of your SOP when you start writing.
- Whoever would read that SOP, would probably like to know it’s purpose. In two sentences describe the aim of this document.
- Make sure your SOP includes a title page, by giving the specific name of the process, the name of the department that the SOP applies to, etc.
- It is good to have a table of content because if the document is longer than average, it will be easier to navigate through.
- Incorporate Procedure Scope, only if it’s needed – because some processes can stretch onto different departments or teams.
- Sometimes terminology should be included as well in case there is any complicated term. It should be defined, explained. Also, abbreviations and acronyms should be included there as well.
- The main thing, the core of the document - described procedures, written as simple as possible.
- Set up a meeting and ask employees to take you through the process step by step in procedures, to make sure you are all on the same page.
- Make sure it describes procedure specific to a particular task where it is a must to be performed correctly and in a proper manner form.
- Provide clear and definite instructions so that procedure is undoubtful, uncomplicated, well elaborated, and adaptable.
- Very often it does look like a checklist. But depending on the workplace, they tend to be limiting. The alternative to this is usually a workflow diagram or flowchart as a visual explainer for procedures.
- Do not forget any supplementary information that can include just anything, of course, depending on the process. To give you an idea, it could be information on some device or equipment, health, and safety warning, etc.
- Involving metrics could be handy if the measuring efficiency would contribute to improvement.
- When you have it all gathered, in one document, it’s time to go from theory to practice, in another word, implementation of the things that you have written.
- There is an option to do a test version. Hand it out to departments and see if they break.
- Of course, make it easily accessible to all your employees.
- It always should be somewhere visible for the employees or it’s can be online if that is more convenient.
- That is one of the first questions that auditors would ask to see on their visit.
- It wouldn’t be bad if it would be reviewed from time to time in case some changes happened during the time.
- Every process should have a process owner who is accountable for updating it periodically to make sure it matches the current process.
We all like to see examples, so there is one from FDA - https://www.fda.gov/media/73789/download
We are aware that it might still look complicated to you, but trust us, it’s not complicated at all if you manage your quality management system with the right eQMS.
Do not hesitate to get in touch with us and let us help you out.
Simon B.
|