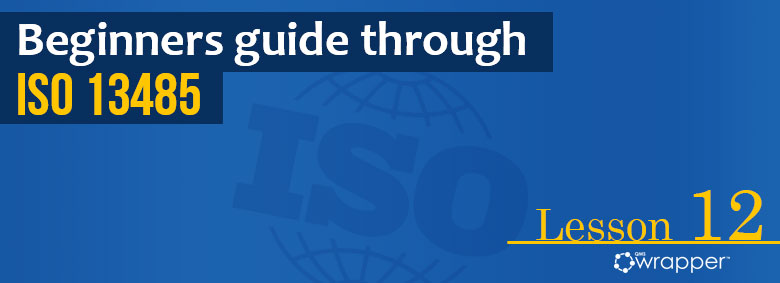
From A to Z about Design and Development of medical device ISO 13485:2016 – Lesson 12
The design and development of the medical device are one of the most crucial parts of the ISO 13485 standard due to its complexity compared to other industries. The design and development process for medical devices has to deal with product safety, risk controls, relevant regulations, and customer needs. On one hand, it’s a continuation of the previous lesson based on customer needs and requirements that you included in the D&D process. The point is that if you as a medical device company fail to meet regulatory design requirements, it won’t be able to reach the market.
Because Design and development processes include planning, inputs, outputs, review, verification, validation, transfer, control of D&D changes, and design and development files.
Design and development planning
The first and most important stage is planning because good planning will take you through with no additional costs or delays through the development of your medical device. For reason, it's said good planning is the first step to success. In this planning phase, you will set your goals of the design and development of your product, set certain activities that will include risk management. Point is to implement quality control through the design and development process as well.
The tactic is to examine whether the development advances within measured steps according to prior planning. It is important to update the plan as the development advances and to change the plan according to what is required.
Someone with expertise must be appointed who will be managing the process. The planning process additionally should include verification, validation, and design transfer including traceability design and development activities.
Design and development inputs
If there are quality inputs, there will be quality outputs. Simple as that. It’s crucial to adequately evaluate the needs of the customers and determine the inputs for the medical device carefully. Things like: intended application, past complaints, risk control, physical features, safety factors, etc. should be included while collecting inputs as well. The ISO 13485 standard requires functionality, performance, and safety according to the intended use. Plus, they must be reviewed and approved by appropriate resources for accuracy and completeness.
Design and development outputs
Outputs now should carry out input requirements. It’s expected they will provide appropriate information for purchasing, production, and service provision. Moreover, it should specify the characteristics of the product that are essentials for its safe and proper use. To clarify, design output is a drawing or specification or manufacturing instruction. It consists of described parts, pieces, and components of the medical device.
As required from the ISO 13485 standard, any output of design and development stages naturally has to be properly documented and approved.
Design and development review
Design and development review practically should be performed after each step in the Design Controls. In a certain way, it should be synchronized with design and development planning. The aim is to evaluate the design and development results if they meet the requirements and to identify and propose necessary actions. For the success of medical device development, reviews in these stages are crucial. On top of that, the level of complexity and formality of the review will be determined according to the nature of the medical device. The most important is that records of the results of the review and necessary actions are maintained.
Design and development verification
If you have done everything so far right, in this stage demonstrate you will demonstrate that you have designed your medical device correctly. How? By conducting some tests, inspections, comparisons, or analysis to show your design and development outputs met design and development inputs. Verification is a mandatory requirement and the records on verification results should be maintained.
Design and development validation
Validation means demonstrating that you have designed the product you intended to. Validation indicates that your outputs and resulting product meet the specification of functionality, performance, safety, and intended use. It should ensure the medical device satisfies its user's needs. Of course, validation activities should be recorded along the process.
Design and development transfer
The transfer of a product design into a manufacturing environment requires a detailed set of processes to organize many tasks at the same time. The keys to an effective transition are experience, well-defined, then executed procedure, and cautious review. This should ensure the transfer of a medical device product and related processes from the development phase to manufacturing in advance of product launch and commercialization.
Control of design and development changes
Changes are likely to happen during the design and development process, and the medical device companies are required to establish a way to control such changes. Every change should be evaluated based on the impact on all aspects of the medical device. The goal is that change is introduced throughout the entire development process. Records on any change, its review, and necessary actions should be maintained.
Design and development files
This is the so-called DHF or Design History File as per the FDA. As per this standard is the design and development Files. This part of the standard again shouts out that everything, but everything needs to be documented. It always has to be up to date so it can represent the current product including all changes. The file may include reference records of conformity to design requirements, records of review, verification, validation, and changes.
qmsWrappers Traceability Matrix has an innovative and unique approach
to manage complex medical device products, where users can have
a quick and clear overview of their medical device life-cycle.
The importance of the Traceability Matrix stems from the fact that it connects
requirements and uses cases to design inputs, outputs, verification,
validation, and Risk Management. It’s central to the development
of safe medical devices and, when it’s done right, it’s the foundation
of your FDA Design History File (DHF) and your CE Mark Technical File (TF).
PREVIOUS LESSON NEXT LESSON ALL LESSONS
Aaron Lui
|
qmsWrapper team
|
Hi Lui, with a good tool, design control doesn’t have to be a nightmare. Try our software (Free Trial is 14 days) and you will see why Traceability Matrix is one of the favorite features of the software for our users.