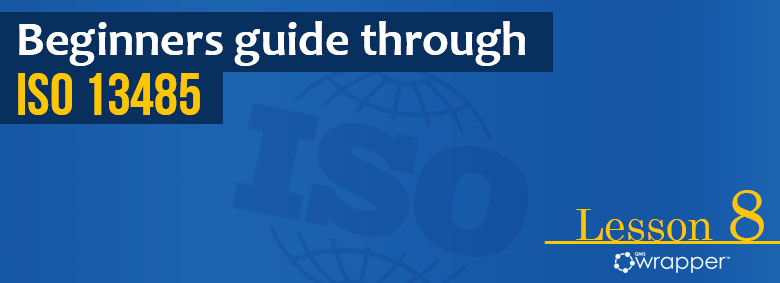
What is Resource Management in the medical device world – Lesson 8
As a requirement within ISO 13485, the management must ensure that adequate resources are available to perform continuous work by the organization. Providing resources can refer to personnel, infrastructure, consumables, equipment, etc.
Human resources
In this part, the standard focuses on the improvement of human resources by making sure they can provide quality work. It’s very important the connection between qualified employees, the implementation of QMS, and maintenance of its effectiveness. For success, a medical device company has to combine human resources and knowledge, in other words, the training of employees is unavoidable. Auditors and FDA inspectors are usually asking for evidence of it. That’s why there is a saying: “if it’s not documented, it’s as it didn’t happen”.
Some elements and job characteristics must be defined and documented, as ISO 13485 obliges, like education, regulatory requirements, experience, certification, and training.
When we come to training, you have to know that every type of training has a specific goal that supports or/and promotes the organization’s values. Also, training has to fill the gaps between the current skills and the desired skills. The organization can provide training in several ways like frontal, e-learning, external, or even visits to suppliers’ facilities.
At the end of the training, it’s always necessary to evaluate its effectiveness. It has to be done periodically and should include physical examinations.
qmsWrapper comes with default made processes based on ISO 13485 requirements,
including the “Competence, training and awareness”.
That will make it easier to record training requirements, proving it's held,
and to perform effectiveness evaluation as the final step.
Infrastructure
This part includes the building, workspaces, process equipment, software to support business operations and support services. They are expected to be appropriate and are properly maintained to achieve conformity to product requirements. Maintenance of buildings and facilities is performed by external contractors. This includes regular checking on lighting systems, air conditioning, and heating systems.
Using qmsWrapper’s Custom form feature it is easy to build
the template for recording the maintenance activities.
It will be obvious that who and when performed it,
therefore it's easier to follow up when the next interval
of maintaining certain activities shall be done.
Here is also important to note that the medical device company must document the requirements of their infrastructure to achieve conformity to product requirements and prevent product mix-ups ensuring orderly product handling.
PREVIOUS LESSON NEXT LESSON ALL LESSONS
ISO 13485 implementation: Mandatory documents and records
Validation efforts
Gap analysis in QMS