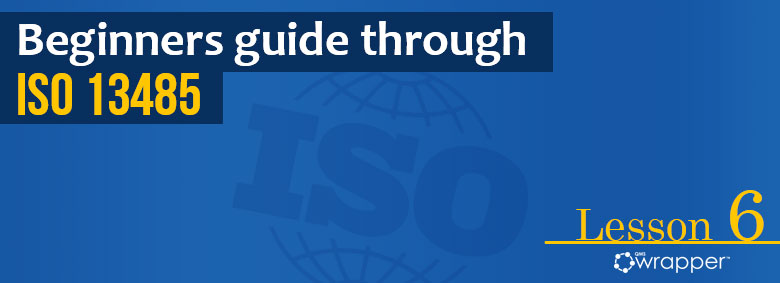
Responsibility, authority, and communication in ISO 13485 – Lesson 6
Responsibility and Authority
Top management is in charge of appointing responsibilities to other staff and management to ensure that the QMS is being met. They also need to be responsible for communicating internally.
One of the musts for them is to establish the pyramid of decision making to accomplish the quality objectives. ISO 13485 emphasizes the fact that they have to identify the training and qualifications needed for each function.
In every medical device company, there must be an organizational structure. It describes roles, functions, and relations it shows who reports to whom. Every defined role must have a job description in which will be defined its responsibilities and authorities. Naturally, top management has to ensure every employee is aware of its duties and responsibilities.
Management Representative
Top management is moreover in charge to appoint a member of management who has the authority and responsibility to:
• ensure the processes needed for the QMS are documented
• report to top management on the effectiveness of the QMS
• ensure promotion and awareness of the QMS throughout the organization
By all means, he is in charge of the entire QMS. He/She is like a living spine of the system and will undertake the ultimate responsibility for its effectiveness. It’s expected that person has the most knowledge of the ISO 13485 standard in the company. It is his / her duty to ensure the documentation is compliant with the requirements of the standard.
It is important to bear in mind that the Management Representative does not have to be dedicated only to quality, specifically the standard notes they may have other responsibilities.
Internal Communication
It’s one of the vital factors, and it has one of the most important roles in any organization. In other words, it’s effectiveness. Effective communication will allow the efficient flow of data.
Internal communication regarding the quality management system flows two ways:
- The management communicates to the organization the quality policy and objectives; customer and regulatory requirements; product and process specifications; verification and validation requirements; and instructions on how to implement and use the quality system.
- The organization communicates to the management information and data regarding quality performance and the effectiveness of the quality system
Management sets Quality Objectives and has to communicate those. These objectives have metrics and targets (e.g. scrap, customer complaints per month, resolution time for complaints) and potentially some kind of charting/graphing / tracking over time.
For all team members to work towards the same objectives and targets, management has to communicate those to every team member and explain how they can contribute to reaching these targets (example: daily team meetings, newsletters, an information board in the break room, walk-about board).
The effectiveness of the QMS is determined by meeting the targets.
Any information can be communicated through:
- Paper or electronic documents, such as manuals, procedures, instructions, drawings, specifications, quality records, reports, etc.;
- E-mails, memos, and meetings;
- Bulletin boards and the intranet site and newsletter;
- Training and awareness programs; and
- Employee suggestions, surveys and, feedback
qmsWrapper’s chat is a purpose-built Team Collaboration that maintains compliance built into its DNA to help foster and support team based regulatory compliance.
Also, assigning tasks between members of a certain project in qmsWrapper is a way of communication that addresses a certain assignment.
PREVIOUS LESSON NEXT LESSON ALL LESSONS
Emma
|
Emma
|
Emma
|