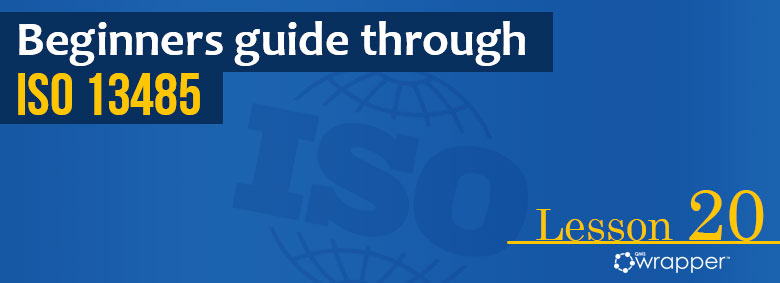
Improvement through corrective and preventive action – Lesson 20
The ISO 13485 standard in this lesson wants to suggest you a few explanatory perspectives that may serve as inputs for improvement. It also expects you to define which inputs, and sources of information may indicate the need for improvement.
From your medical device company is required to initiate the link between quality activities such as quality policy, quality objectives, audit results, CAPAs, etc. and the systematical improvement. By this is meant to identify the relevant parties, processes, records, and outputs of these activities, collect the crucial data, evaluate the need for change, and decide whether the improvement is necessary or not.
Corrective action
One of the foundation elements of quality and also essential management for sustaining improvement is corrective action.
Corrective action promotes a systematic analysis of quality problems that have already occurred and the elimination of any root causes of nonconformities through the implementation of controlled measures.
The initiation of corrective action involves all levels of the medical device company – management, design, and development, purchase, production, collection, quality, service, and logistics. It's done methodically through the documented procedure.
In practice, the planning of the corrective action is to be documented and will serve as a quality record. The record may appear as a work plan, a project plan, or refer to such dossiers. Plus, it’s required to review and verify the effectiveness of the corrective action.
Preventive action
What is the difference between corrective and preventive action? Corrective action addresses existential nonconformities – that is, the nonconformity occurred and was detected. A preventive action Is a quality tool for protecting medical devices from nonconformities - that is evaluating risks and potential events that may affect the quality of the medical device.
Think this way - the nonconformity has not yet occurred, but you know that it may—this is the time to capture and submit it to a controlled process.
By using traditional methods of identifying problems early, you will implement systematic quality tools that may ensure the liability and dependability of processes and maintain the quality of the medical device.
The process of evaluation of a root cause of a potential nonconformity is identical to the evaluation of a root cause of an occurred nonconformity. And as it is with corrective action, it’s the same with the preventive action it must be documented. The main goals of these records are monitoring and control.
There is a lot of different solution for documenting and controlling corrective and preventive actions – from the simple traditional forms to sophisticated designated software, such as qmsWrapper.
As a medical device company, you need to find an appropriate solution for your organization and the nature of your process.
qmsWrapper provides a process for CAPA, that make sure non-step will be missed when it comes to this quality event. It will ensure the nonconforming event will be recorded, the action to eliminate such event will be defined, as well the action to prevent its re-occurrence and at the end, that it will be verified the actions don’t adversely affect the ability the regulatory requirements will be met or the safety and performance of the device would be affected.
PREVIOUS LESSON NEXT LESSON ALL LESSONS
Sofia Nascetti
|
qmsWrapper team
|
Hi Sofia, we completely agree with you. qmsWrapper is process-based, so you won't miss a single step of a particular process. Try our software for free: https://store.qmswrapper.com/