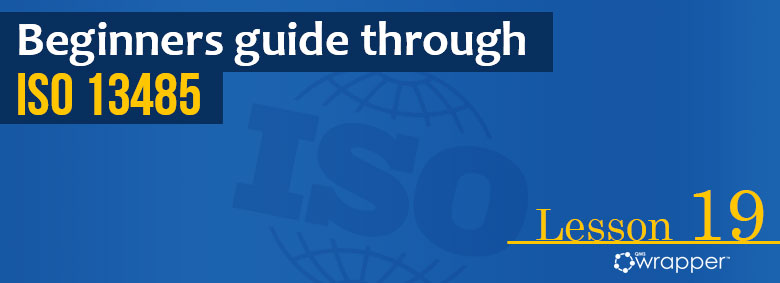
What ISO 13485 considers under - Analysis of data? – Lesson 19
The ISO 13485 Standard requires collecting data from processes and activities and analyzing them to identify trends and patterns in your processes to verify the continuing suitability and control of the effectiveness of your QMS by maintaining improvement.
It’s advisable to ask a lot of “how” based questions when analyzing your quality management system.
The data analysis includes an examination of the effectiveness, information, and data gathered from various resources, generated from customer feedback, etc.
Data analysis aims to see or check on your QMS effectiveness. It’s most practicable to achieve it by setting goals and measure their fulfillment or improvement. Popular improvement operations can be CAPA, changes as a result of customer complaints, and advisory notices.
Once an improvement has been initiated and implemented, the analysis of data is a tool that can be used to evaluate whether improvement activities have been successful and have achieved their goals.
Strategy for identifying the data for analysis
The data analysis should relate to the issues relevant to the performance of your QMS. These issues will be inputs for the data analysis. The requirements for data resources are the controls that were suggested throughout the standard. For example:
- Human resources
- Work environment
- Substructures
- Product quality planning
- Control of product and processes
- Design and development plans
- Risk control performances
- Validation and verification, etc
From these issues, you need to identify which processes trigger data that can be analyzed. The evaluation of each data will give you an answer to the requirements above. The analysis of the data will allow you to detect trends and patterns occurring on your processes that require attention.
You need to determine which kind of data will work out for you the best and then decide how it can be gathered. Keep in mind that your data do not to be statistical. Some processes can be shown in numbers and some cannot.
Determine the method and technique for analyzing the data. The purpose of the technique is to objectively demonstrate through data that processes meet their specifications.
Records
The recording is a must as usual as per ISO 13485. Remember, every medical device company has to document almost everything. The records will prove that the data was gathered and analyzed according to your defined method.
qmsWrapper provides Search and Report tool that allows you to extract data collected during processes, so the analysis, if the quality management system is suitable, adequate, and effective, is very easy. Search results can be exported, so you can get the report on a click!
PREVIOUS LESSON NEXT LESSON ALL LESSONS
Rishav T.
|